INNOVATION BREAKTHROUGH FOR EVOLVE DYNAMICS
A significant new milestone has been reached by the Research and Development (R&D) team at Evolve Dynamics as they have successfully utilised metal (titanium) 3D printing for the first time. This technology, which is otherwise acknowledged within industry as Direct Metal Laser Sintering (DMLS), has produced titanium and aluminium components for the company’s SKY MANTIS HEAVY aircraft.
Already used widely in the defence and aerospace industries and prevalent across other sectors such as Formula 1, 3D printing represents the cutting edge of Design for Manufacturing (DFM). This innovation allows engineers to optimise their designs without being bound by the limitations of traditional machining with Computer Numerical Control (CNC).
By controlling quality and consistency, DFM techniques are utilised by engineers to lower the cost and increase the pace of the manufacturing process. This recent technological breakthrough delivers a number of advantages to a business, including the following:
– Less waste and cheaper to manufacture compared to alternative manufacturing methods.
– A quicker turnaround following request, resulting in a lower lead time.
– The ability to iterate product with greater ease and at increased pace.
HOW DOES THIS INNOVATION BENEFIT THE AIRCRAFT?
Thanks to DMLS printing capabilities, it has been possible to manufacture shoulder leg mounts for SKY MANTIS HEAVY without compromising the aircraft’s manoeuvrability and flight time. Without this innovation, the team would have had to redesign a new set of parts, which would have been bulkier, heavier, and more complex to assemble and service.
WHAT ARE THE BENEFITS TO THE END USER?
This technology enables bolder designs to be developed and optimised. As the cost to manufacture is reduced, it is likely that this fall in price will also ultimately be felt by the customer. 3D printing technology delivers lower lead times, which helps to get the product out to the customer in quicker time.
WHAT NEXT?
The team has so far produced parts in titanium and AlSi10Mg – an alloy of aluminium, silicon, and magnesium – which is used in aerospace, F1, and healthtech.
We’re pleased to say that the company is only at the beginning of this particular innovation journey. In the coming weeks and months, the team anticipates adopting the use of DMLS printing technology for the manufacture of motor mounts on the company’s SKY MANTIS 2 and for shock-absorbing landing gear (SALG) shoulder brackets. Watch this space.
Lawrence Hulse, Senior Mechanical Design Engineer at Evolve Dynamics commented:
“This is an important technology for the business and the wider UAV sector. 3D printing capabilities are enabling us to deliver technological change at a quicker pace, whilst empowering the team to optimise the strength, functionality and weight of components. The manufacturing process ultimately becomes simpler and more cost effective as a result”.
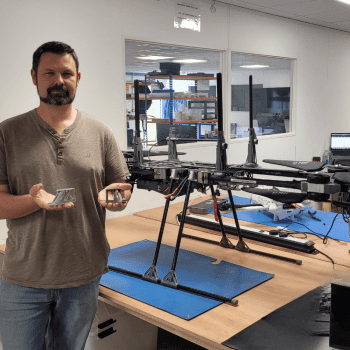
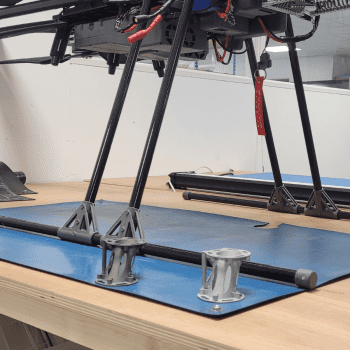